ERZlich Willkommen liebe Freunde der Schutz-, Leit- und Elektrotechnik. In unserem neuen Fachbeitrag geben uns Roland Bürger (MBS AG) und Klaus Behringer (Ingenieurbüro Beyer) spannende Einblicke in neue Möglichkeiten zur zustandsbasierten Wiederholungsprüfung mittels Differenzstrommonitoring und ganz nebenbei gibt es einige wichtige Grundlagen zur DGUV-V3. Viel Spaß beim Lesen und los geht's!
Zustandsbasierte Wiederholungsprüfung für ortsfeste Anlagen gem. DGUV V3 durch Differenzstrommonitoring
Eine Anlagenprüfung wurde bereits in der ersten VDE-Vorschrift aus dem Jahr 1896 gefordert. Mittlerweile wird die Anlagenprüfung für neue und erweiterte Anlagen in der DIN VDE 0100-600 beschrieben. Wiederkehrende Prüfungen werden in der DIN VDE 0105-100/A1 mit Verweisen auf die DIN VDE 0100-600 normativ erfasst. Darüber hinaus wird die Wiederkehrende Prüfung auch in dem Regelwerk DGUV Vorschrift 3 (ehemals BGV A3) beschrieben und gefordert. Die Abkürzung DGUV steht für die Deutsche Gesetzliche Unfallversicherung. Dieser Verband besteht aus 27 Unfallkassen und neun gewerblichen Berufsgenossenschaften. Hier werden derzeit ca. 70 Millionen Menschen gegen die Folgen von Arbeitsunfällen und Berufskrankheiten versichert. Die Vorschrift 3 der DGUV beschreibt die Prüfung von elektrischen Betriebsmitteln und Anlagen, die in den Betrieben eingesetzt werden. Die Absicht dieser Vorschrift ist, dass sich die Anlagen in einem ordnungsgemäßen Zustand befinden. So wird das Risiko von Personenunfällen, elektrisch gezündeten Bränden oder Anlagenschäden minimiert.
Da es sich bei der DGUV-V3-Prüfung um eine gesetzliche Vorschrift handelt, sind Unternehmen dazu verpflichtet, diese Prüfung durchzuführen. Versicherungen verweigern im Falle eines Schadens regelmäßig die Zahlung von Leistungen, wenn kein Nachweis über die fristgemäße Prüfung des schadensverursachenden Betriebsmittels vorliegt. Selbst die Kündigung von Policen ist in schwerwiegenden Fällen keine Seltenheit. Dem Unternehmen drohen außer den Ausfällen und Kosten eventuell noch zusätzlich existenzgefährdende Klagen auf Schadensersatz.
So nachvollziehbar diese Vorschrift auch erscheinen mag, so verursacht sie nicht nur erhebliche Kosten für die Betreiber elektrischer Anlagen und ortsfester Maschinen. Für die Prüfung werden oftmals die Anlagen und Maschinen abgeschaltet, um die Isolationsmessung durchzuführen bzw. die Schutzeinrichtungen (z. B. RCDs) zu testen. Die zeitlichen Intervalle für die wiederkehrende Prüfung sind in der DGUV Vorschrift 3 in der Tabelle 1 A aufgelistet. Eine in der Praxis oft diskutierte Frage ist, ob es sich bei den genannten Prüffristen um gesetzliche Vorgaben oder lediglich um Richtwerte handelt.
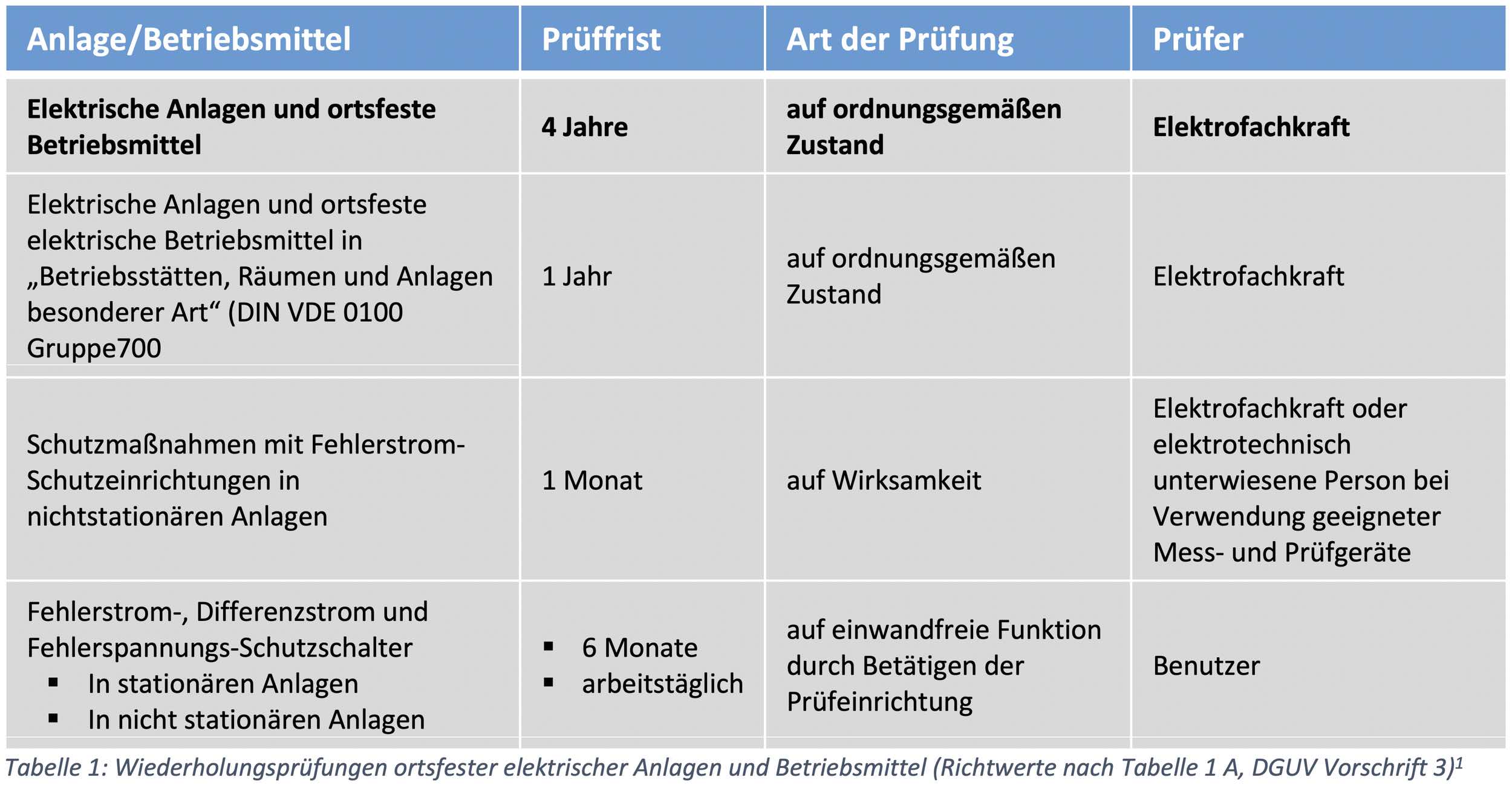
In der DGUV Vorschrift 3 heißt es wörtlich unter § 5 Prüfungen:
„Der Unternehmer hat dafür zu sorgen, dass die elektrischen Anlagen und Betriebsmittel auf ihren ordnungsgemäßen Zustand geprüft werden
1. Vor der ersten Inbetriebnahme und nach einer Änderung oder Instandhaltung vor der Wiederinbetriebnahme durch eine Elektrofachkraft oder unter Leitung und Aufsicht einer Elektrofachkraft
und
2. in bestimmten Zeitabständen
Die Fristen sind so zu bemessen, dass entstehende Mängel, mit denen gerechnet werden muss, rechtzeitig festgestellt werden.“
Nach Auskunft der BG ETEM /2/ handelt es sich in der Tabelle 1 A der DGUV Vorschrift 3 um Richtwerte, die sich über Jahre etabliert haben.
Auch in der Arbeitsstättenverordnung (ArbStättV) werden die bewährten Prüffristen oftmals nur empfohlen. Es stellt sich nun die Frage auf welcher Grundlage die Prüffristen der ortsfesten Anlagen bemessen werden sollen, wenn es sich bei den Werten in der Tabelle 1 lediglich um Richtwerte handelt. Ein Abweichen von den vorgeschlagenen Prüffristen sollte im Bedarfsfall begründbar sein. Hinweise in der DGUV Vorschrift 3 sucht man vergeblich. Seit der Veröffentlichung im Jahr 1979 hat es keine Änderung dieser Vorschrift gegeben. Hilfreich ist die deutlich jüngere DGUV Information 203-071 /3/ (Ausgabedatum 2020.01). Hier heißt es unter Punkt 7 „Prüffristen“ /4/:
„Das Festlegen der Prüffristen im Rahmen der Gefährdungsbeurteilung liegt in der Verantwortung des Unternehmers. Die Gefährdungsbeurteilung muss fachkundig durchgeführt werden … Prüffristen sind unter Berücksichtigung der konkreten betrieblichen Situation beim Betrieb der Anlagen und Betriebsmittel zu ermitteln und in der jeweiligen Gefährdungsbeurteilung festzulegen. … Als Entscheidungshilfe für die Festlegung von Prüffristen können die Empfehlungen aus den Durchführungsanweisungen zu §5 der DGUV Vorschrift 3 und 4 herangezogen werden. Diese Werte sind Richtwerte für normale Betriebs- und Umgebungsbedingungen und haben einen orientierenden Charakter. Eine ungeprüfte Übernahme der vorgeschlagenen Prüffristen ohne Berücksichtigung der eigenen betrieblichen Situation kann bei zu langen Prüffristen dazu führen, dass gefährliche Mängel nicht rechtzeitig festgestellt werden. …“
Unter diesem Text ist noch der bereits bekannte Hinweis aus der DGUV Vorschrift 3 angeführt:
„Prüffristen sind keine Wunschfristen! Die Fristen sind so zu bemessen, dass entstehende Mängel, mit denen gerechnet werden muss, rechtzeitig festgestellt werden. (§5, Abs. 1,2. DGUV Vorschrift 3 und 4)“
Das Kapitel schließt mit der folgenden Feststellung.
„Diese Forderung kann dazu führen, dass die tatsächlichen Prüffristen gegenüber den Richtwerten der Tabellen je nach betrieblicher Situation deutlich verkürzt werden müssen oder aber verlängert werden können.“
Grundlage für die zu ermittelnden Prüffristen ist nach den obigen Ausführungen eine Gefährdungsbeurteilung gem. TRBS 1111 /5/. Hierbei können durchaus Prüffristen ermittelt werden, die über die vorgeschlagenen vier Jahre hinausgehen. Dies ist nach dem DGUV Regelwerk also zulässig. Trotz der regelgerechten Festlegung der Prüffrist für die Wiederholungsprüfung kann die Anlage bzw. Maschine durch nicht vorhersehbare Umstände ausfallen. Um diesem Scenario entgegen zu wirken wird in einigen innovativen Industriebereichen bzw. kritischen Liegenschaften bereits die vorausschauende Wartung (englisch: Predictive Maintenance) praktiziert. Auf Grundlage von gewonnenen Zustandsdaten per Sensoren können die Inspektions- oder Wartungszeitpunkte einer Maschine bzw. Anlage präzise prognostiziert werden.
Im Bereich der elektrischen Installation können unvorhergesehene Schäden in der Isolation mittels einer kontinuierlichen Differenzstrommessung rechtzeitig festgestellt werden, so kann die Wiederholungsprüfung bei erhöhten Differenzstromwerten vorgezogen werden. Meist kann dadurch eine unkontrollierte Abschaltung der Anlage verhindert werden.
Die kontinuierliche Differenzstrommessung ist bereits für den Neubau von Rechenzentren verpflichtend vorgeschrieben (DIN EN 50600-2-2). Der Differenzstrom wird hierbei als Kennwert für den Zustand der Isolierung der Anlage verwendet. In einem aktuellen Projekt konnte der Betreiber schadhafte Schaltnetzteile frühzeitig über erhöhte Differenzstrompegel detektieren und rechtzeitig für Ersatz sorgen. Eine unkontrollierte Abschaltung verschiedener Server konnte somit verhindert werden.
Ein willkommener Nebeneffekt ist, dass eine Prüfung der Isolation gem. DGUV Vorschrift 3 entfallen darf.
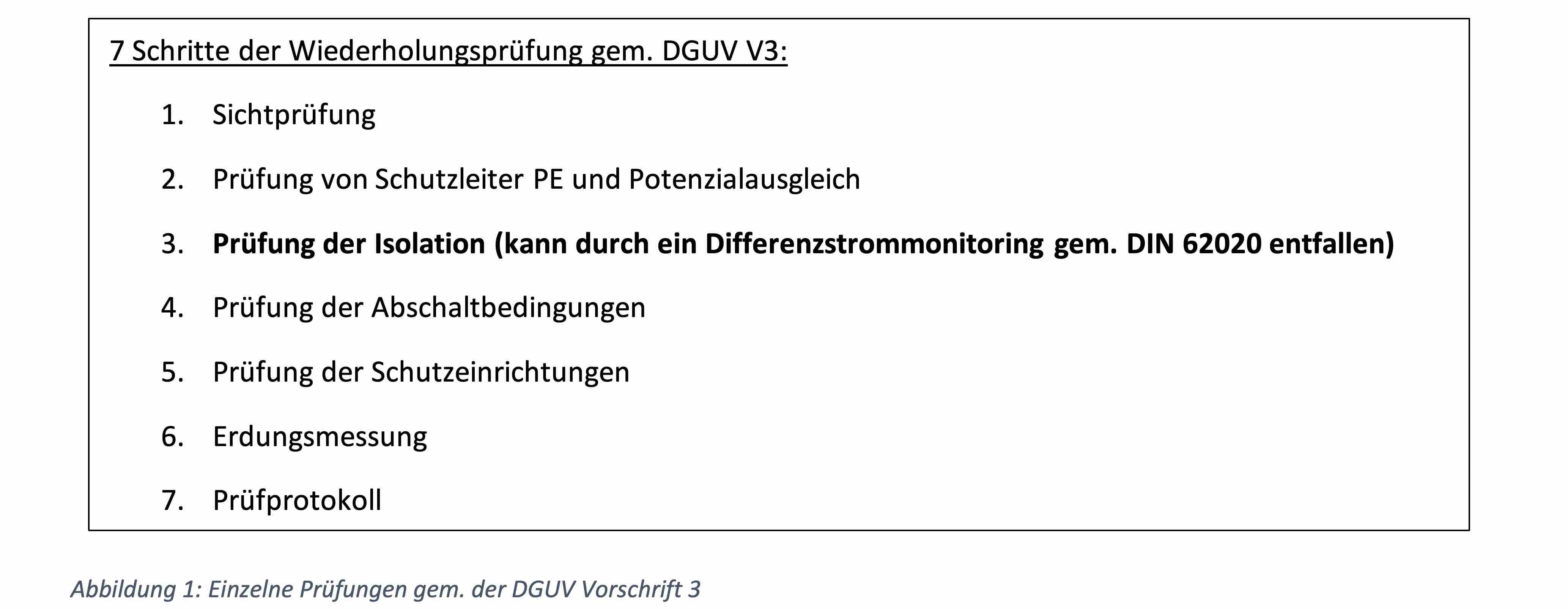
Dieser Sachverhalt ist in der deutschen Norm DIN VDE 0105-100/A1:06/19 dokumentiert. Hierzu heißt es in Abschnitt 5.3.3.101.0.2:
„Wenn ein Stromkreis durch ein Differenzstrom-Überwachungsgerät nach DIN 62020 (VDE 0663) … ständig überwacht wird und diese Überwachungseinrichtungen einwandfrei funktionieren, kann auf die Messung des Isolationswiderstands verzichtet werden.“
Oftmals ist eine herkömmliche Isolationsmessung recht aufwendig. Teilweise müssen Anlagenkomponenten wie Frequenzumrichter oder Schaltnetzteile abgeklemmt werden, weil die empfindlichen Halbleiterbauelemente durch die Prüfspannungen geschädigt werden können.
Erste DGUV V3 Prüfinstitute setzen bereits heute in verschiedenen Industriebereichen auf die Möglichkeit des Differenzstrommonitorings. Durch die Analyse der in Datenbanken aufgezeichneten Messwerte des Differenzstroms kann die Prüffrist der Wiederholungsprüfung gem. der Gefährdungsbeurteilung im Bedarfsfall verkürzt werden. Verschiedene Alarmschwellen lösen Benachrichtigungen per Kurzmitteilung oder E-Mail aus. Die Anlage wird somit einem ständigen Monitoring unterzogen, während die herkömmliche Prüfung des Isolationswiderstandes lediglich eine Momentaufnahme darstellt. Falls die Anlage keine zu prüfende Schutzeinrichtung aufweist, kann auf die Abschaltung in einigen Fällen sogar komplett verzichtet werden.
Neben einigen DGUV Prüfinstituten bieten auch immer mehr Energiemanagement-Anbieter eine kontinuierliche Anlagenüberwachung durch Differenzstrommessung an. Die Wiederholungsprüfung kann dann im Bedarfsfall vorgezogen und ein unkontrolliertes Abschalten oftmals verhindert werden. Für viele Unternehmen ist dies ein deutlicher Fortschritt bezüglich Anlagenüberwachung, Abschaltung der Anlagen und Kosten.
Falls in den Anlagen Schaltnetzteile oder Frequenzumrichter verbaut sind, ist darauf zu achten, dass Differenzströme aus DC- und AC-Anteilen bestehen können. Entsprechende FI-Schutzschalter (RCDs) des Typs B+ können diese nicht-linearen Lasten bereits allumfänglich absichern. Es werden nicht nur DC-Anteile detektiert, sondern es können auch AC-Anteile bis 20 kHz verarbeitet werden. Wird bei diesen Lasten ein Differenzstrommonitor gem. der DIN EN 62020 eingesetzt, sollte dieses Gerät ebenfalls DC-Ströme und AC-Ströme bis mindestens 20 kHz messen können /6/ bzw. siehe hier.
Die MBS-AG bietet für diesen Bereich den neuen Differenzstrommonitor RCMB 70, der sogar den TRMS-Wert bis 100 kHz berechnen kann. Neben einem Relaisausgang mit variablen Auslöseschwellen wird der Messwert als 4-20 mA DC-Standardsignal ausgegeben. Eine Anbindung an Universalmessgeräte mit deutlich niedrigeren Abtastraten oder Feldbussysteme ist damit gewährleistet.
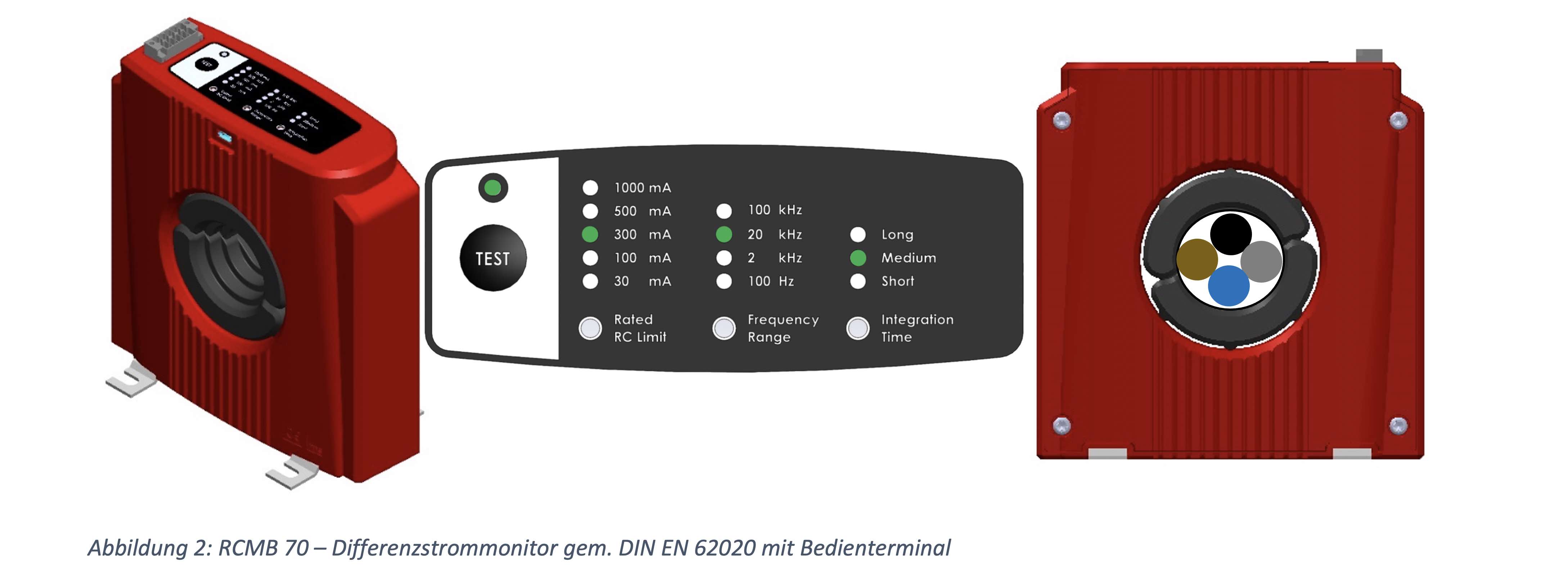
Neben den einzelnen Abgängen kann auch der Zentrale ErdungsPunkt ZEP überwacht werde. Mit Hilfe dieses Wertes kann die Isolation der Gesamtanlage beurteilt werden.
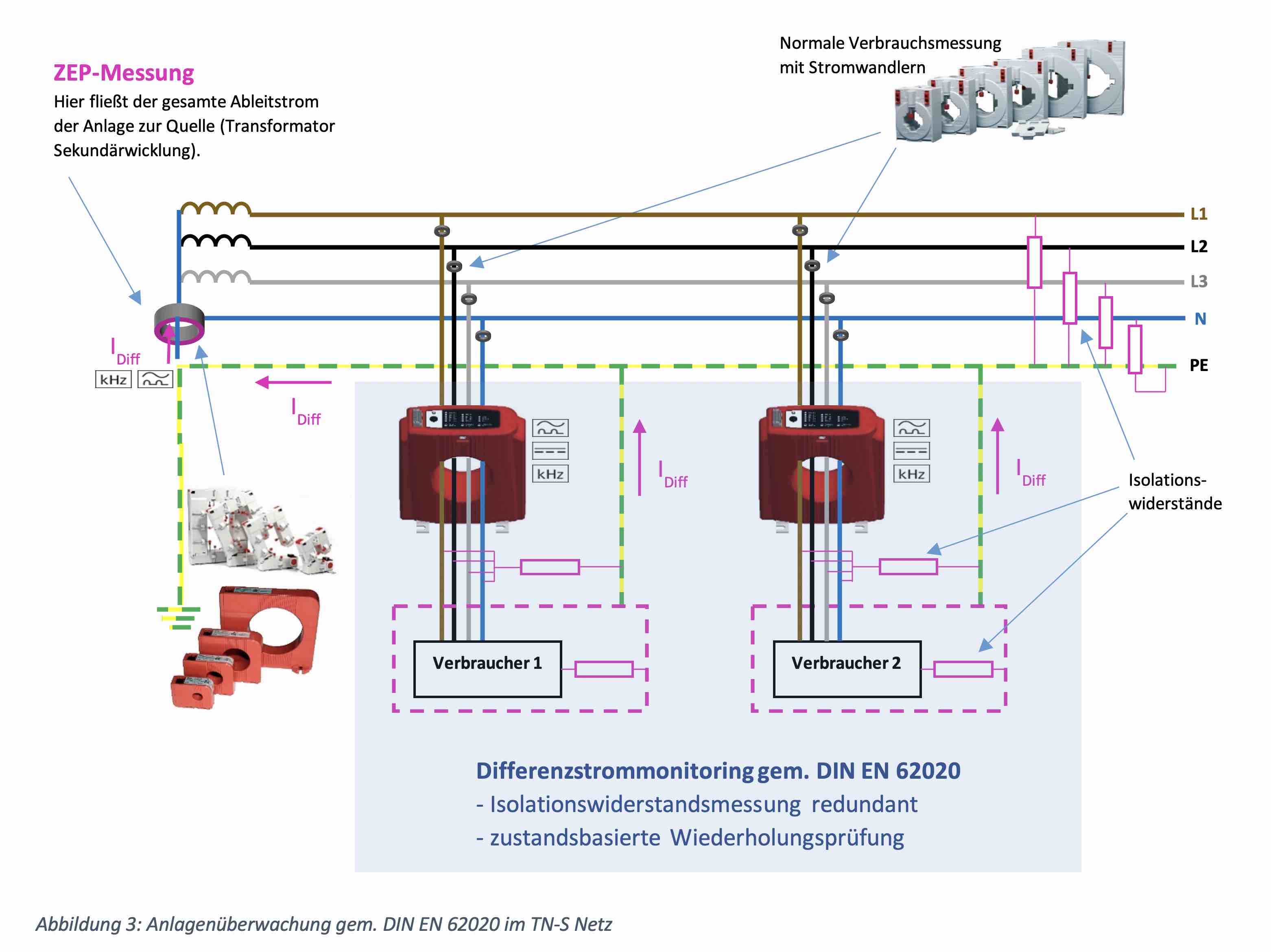
Schauen wir uns Installationen in der Praxis an.
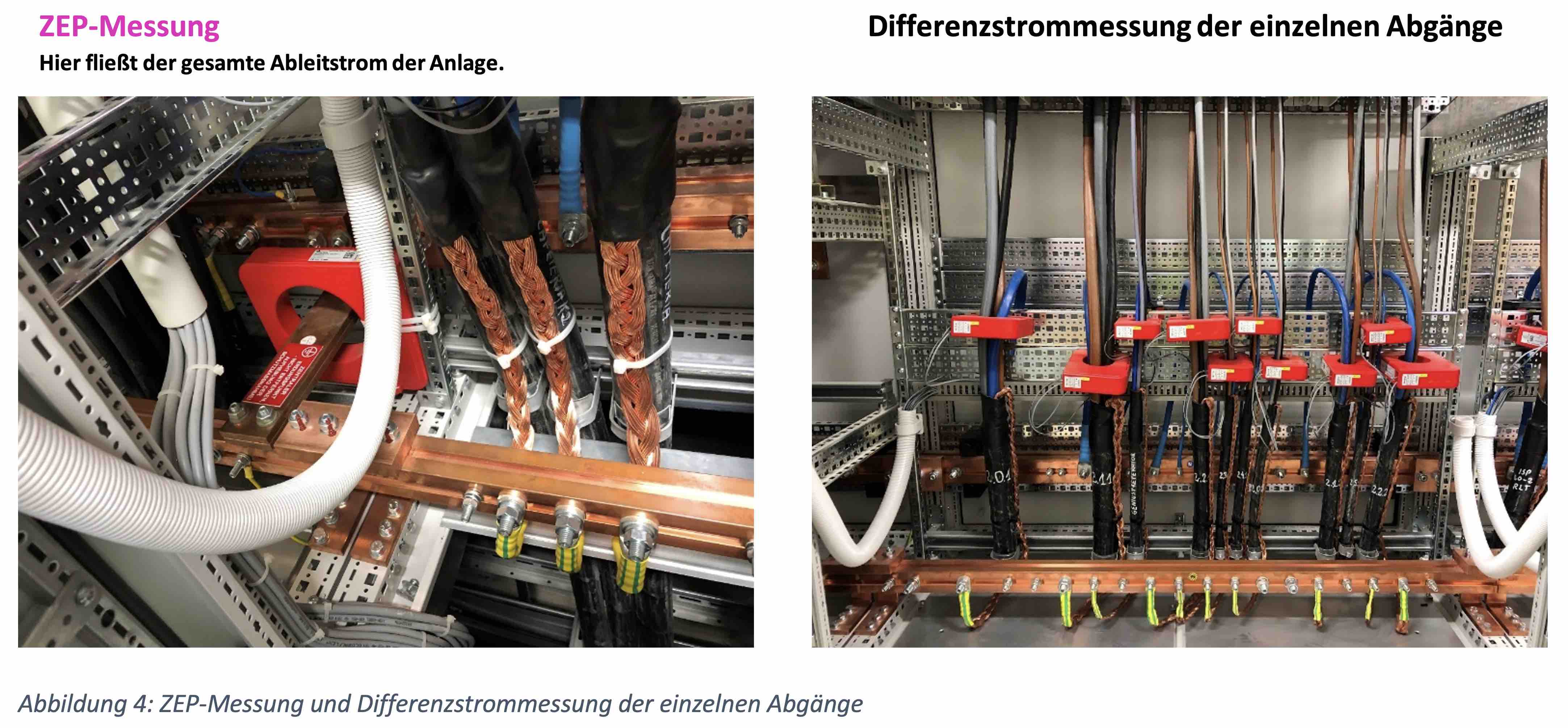
Die Differenzstromwandler wurden in diesem Projekt an Universalmessgeräte von der Firma PQ Plus angeschlossen. Über optionale Module (MMI 12RCM) mit jeweils 12 zusätzlichen Eingängen für Differenzstromsensoren konnte eine für den Kunden optimale und kompakte Differenzstromüberwachung realisiert werden. Über die Software können die Differenzströme eingesehen und mit Alarmschwellen verknüpft werden. Der Anlagenbetreiber und das DGUV V3 Prüfinstitut bekommen bei ansteigenden Differenzstrompegeln eine E-Mail zugesandt.
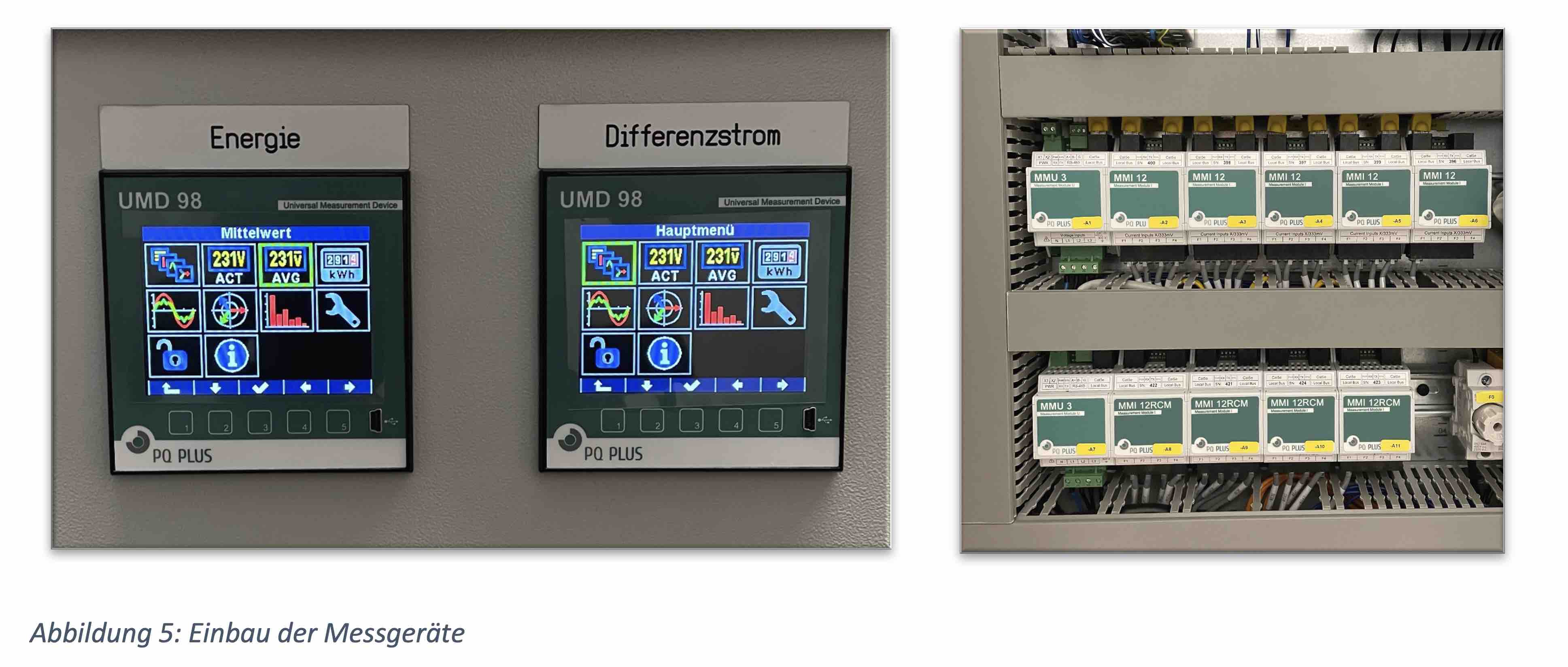
Über die kostenfreie Software ENVIS von PQ Plus können die Alarmschwellen in Abhängigkeit der tatsächlich gemessenen Werte gesetzt werden.
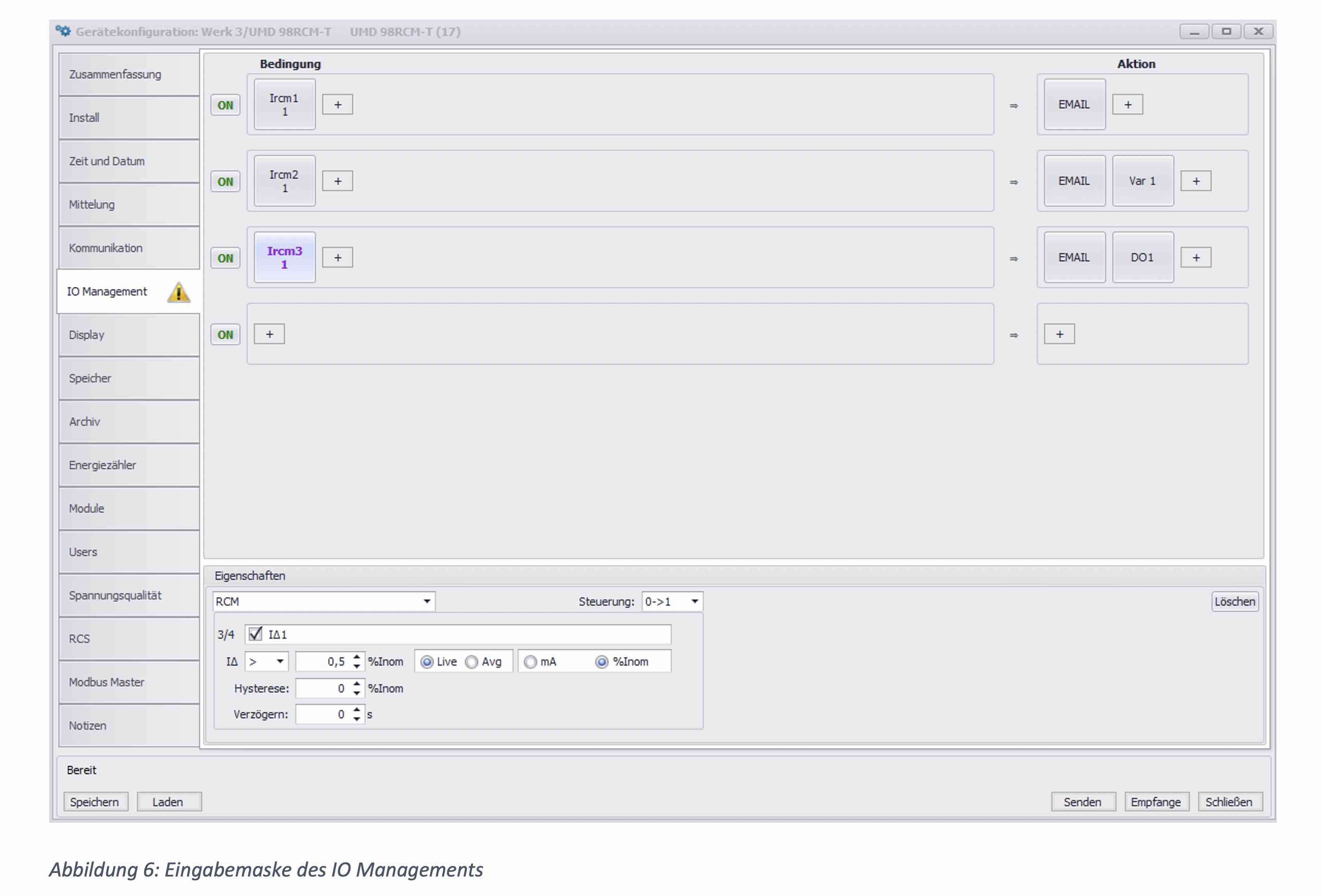
Die zukünftigen Lösungen in der Anlagenüberwachung bedürfen oftmals einer Zusammenarbeit mehrerer Personen unterschiedlicher Unternehmen und Bereiche. Es ist immer wichtig die Bedürfnisse jeder Fachdisziplin ernst zu nehmen und zu verstehen. Nur so können nach deutscher Beamtenmanier wasserdichte Sicherheitskonzepte erarbeitet und gleichzeitig die immensen Vorteile der Automatisierung optimal ausgeschöpft werden.
Für die Unternehmer, die sich auch zukünftig die Wiederholungsprüfung nach DGUV V3 komplett sparen wollen gilt weiterhin das Motto „No risk, no fun!“.
Quellen / Verweise
/1/ https://www.bgw-online.de/Shared Docs/Downloads/DE/Medientypen/ DGUV_vorschrift-regel/DGUV-Vorschrift3_ Unfallverhuetungsvorschrift- elektr-Anlagen-Betriebsmittel-bf_ Download.pdf?__ blob=publicationFile
/2/ https://www.bgetem.de/
/3/ https://publikationen.dguv.de /widgets/pdf/ download/article/787
/4/ https://publikationen.dguv.de /widgets/ pdf/download/ article/787
/5/ Technische Regeln für Betriebs sicherheit, Gefährdungsbeurteilung, TRBS 1111 (Ausgabe: März 2018) https:// www.baua.de/DE/Angebote/ Rechtstexte -und-Technische -Regeln/Regelwerk /TRBS/pdf/ TRBS-1111.pdf? __blob=publicationFile
/6/ Siehe hierzu auch: "Differenzstrommonitoring in der Industrie"
Autoren:
Roland Bürger MBS AG
Klaus Behringer Ing. Büro Beyer